top of page
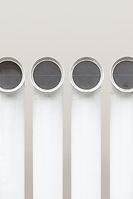
PIPE FUSION
Pipe fusion is commonly used for Geothermal, underground gas lines and underground water lines.
The demand has grown over the years with the durability of this product and its cost effectiveness. To
meet that growing demand Smucker Mechanical has invested in the tools necessary to meet that
demand. Some of the projects we’ve installed is a geo-thermal system with over 40 wells, Underground
gas mains, and water lines for campgrounds. With fusion you don’t have any mechanical joints
underground and the fusion joints are stronger than the pipe itself so you have peace of mind with
installation. Whether it’s a small project or a large project, we have the knowledge, training and
experience to serve you.
The principle behind heat fusion is to heat two surfaces to a designated temperature, and then fuse
them together by application of the required force. This applied force joins the melted surfaces
resulting in a permanent, monolithic fusion joint. PolyPipe® fusion procedures require specific tools
and equipment for the fusion type and for the sizes of pipe and fittings to be joined.
Butt Fusion – This technique consists of heating the squared ends of two pipes, a pipe and fitting, or
two fittings by holding them against a heated plate, removing the plate when the proper melt is
obtained, promptly bringing the ends together and allowing the joint to cool while maintaining the appropriate applied force.
​
Saddle Fusion – This technique involves melting the concave surface of the base of a saddle fitting, while simultaneously melting a matching pattern on the surface of the pipe, bringing the two melted surfaces together and allowing the joint to cool while maintaining the appropriate applied force.
Socket Fusion – This technique involves simultaneously heating the outside surface of a pipe end and the inside surface of a fitting socket, which is sized to be smaller than the smallest outside diameter of the pipe. After the proper melt has been generated at each face to be mated, the two components are joined by inserting the pipe into the fitting. The fusion is formed at the interface resulting from the interference fit. The melts from the two components flow together and fuse as the joint cools.
​
Properly fused PE joints do not leak. If a leak is detected during pneumatic or hydrostatic testing, it is possible for a system failure to occur. Caution should be exercised in approaching a pressurized pipeline and any attempts to correct the leak should not be made until the system has been depressurized.
Note: PE cannot be joined by solvent bonding or threading. Extrusion welding or hot air welding is not recommended for pressure applications.
bottom of page